It's easy to see the benefits of using digital technology to automate your operational pipeline and drive your business forward. But when you decide itâs the right time for your business to go digital, it can be hard to figure out where to start.
With each new client, we like to begin by breaking down âbusiness-as-usualâ activities into workflows and rebuild them on a stronger foundation, ready for automation.
Define.
A clear process
Take time to stand back and assess your full workflow with your team on the ground. Look out for overworked spreadsheets, manual workarounds and missed deadlines - these are big red flags that suggest it might be time to re-evaluate your current process.
Itâs important to understand if all your existing processes are all carried out in the same way by each person.
Take 5 people who do the same job - do they all follow the same steps? Can one person easily pick up where the other left off?
Ask them! Use your teamâs collective knowledge to find the source of inconsistent outputs and anomalies in the way you conduct business.
Your team will have more time to create better outputs, increase your operational efficiency, and help your business grow.
Refine.
Eliminate waste
Once youâve identified the key areas for improvement, the next step is to refine those problematic steps.
You can do this in lots of ways. Here are three of our favourite methods.
The 5 whys.
Root cause analysis that's child's play to implement
Root cause analysis is a very simple and very powerful iterative interrogation technique. It's well worth the effort if you can embed it into your business. Over time the process wonât just help to identify faults but through repetition it will help to prioritise the time you invest improving your process as a whole.
How it works.
This one is pretty simple. You see a problem and ask âWhy?â, then you drill down further to the root cause of the problem by asking âWhy?â a further four times.
Crucially you then share the effort and resources available to resolve the problem evenly across all 5 reasons. You can also collate your 5 reasons over time and youâll then be able to visually identify the critical or recurring faults and tackle those first.
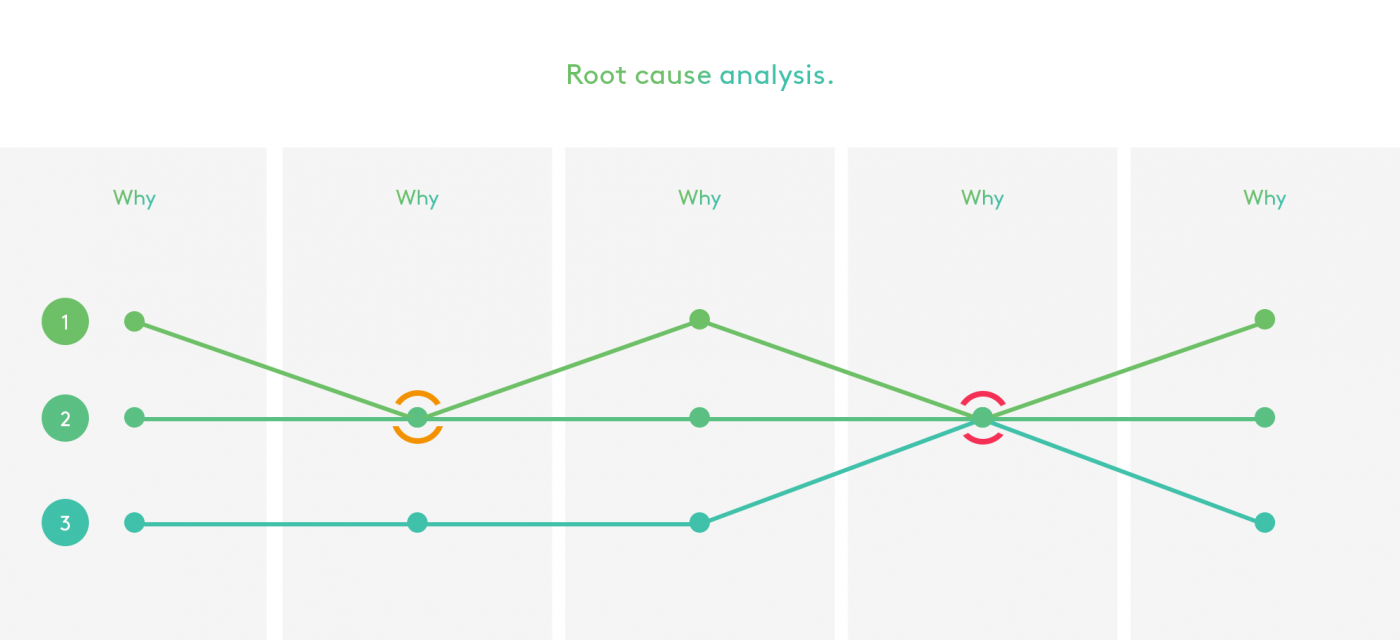
Value Stream Mapping (VSM)
Get your business ready for just-in-time delivery
This method was developed and perfected in Toyotaâs manufacturing plants by Taiichi Ohno in the 1950's. Today, it can help you to analyse your workflow and design a future flow with minimal waste.
How it works.
Value Stream Mapping (VSM) is a direct extension of a simple process map with additional information to determine value and waste.
Take your process map and drill down to add the following details to each action (see our VSM for paper planes below):
- Inputs and outputs
- Responsibilities
- Cycle time - how long does it take the person responsible to complete this specific activity
- Wait time - how long after the previous activity has finished, does the responsible person start the next activity
Adopting a âJust-in-time' management philosophy and applying VSM will allow you to focus on waste reduction. In turn, youâll be able to increase output, reduce downtime and make time for other value-add tasks youâve been meaning to implement.
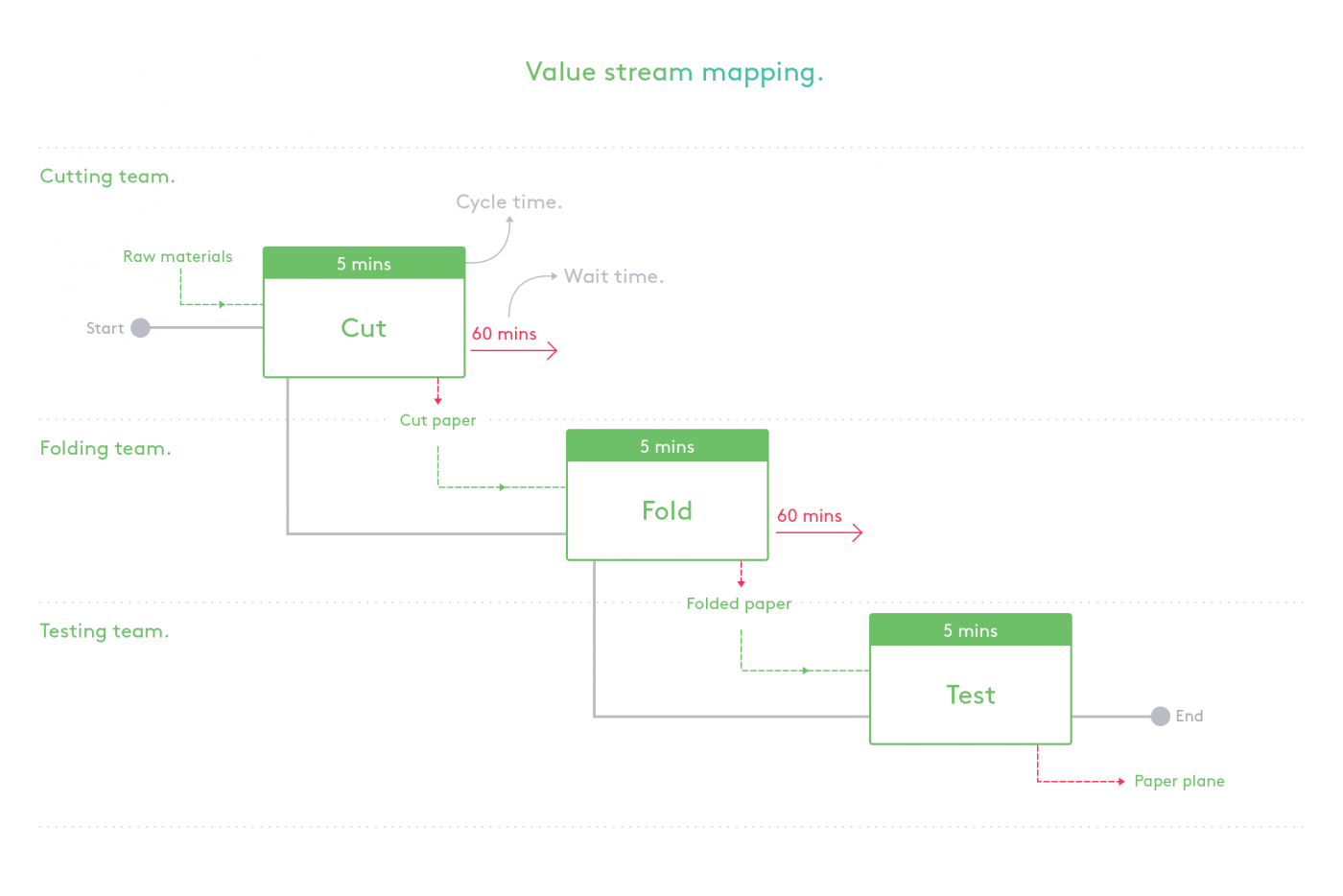
One piece flow.
The beating heart of lean methodology
One Piece Flow is a fundamental part of lean methodology. To think of processing one unit at a time may shock an organisation with batch production at its heart but just watch this short video to see the benefits.â
By reducing the work in progress and using one piece flow you can boost staff moral, reduce the initial wait time and speed up production.
First, automate.
Having identified your causes of waste it's time to remove them
Adopting these techniques isn't just about identifying waste. We've found that they fundamentally change company culture for the better. We have witnessed a clear shift in our clients, in as little as 9 months, from a culture of blame and process for processes sake to a collaborative, solutions first team.
Start with the "we've just always done it this way" processes and get advice from a trusted digital partner that can automate repetitive tasks, integrate existing digital systems and remove manual steps from your process that could be completed more accurately, efficiently or safely when automated.
Then, iterate.
This is only the beginning
People often ask us "If you automate the steps that this team do each day, what will they end up doing?"
The answer is simple - more! Your team will have more time to create better outputs, increase your operational efficiency, and help your business grow.
The outcome of automation is invariable:
- Less waste - therefore better margins
- Less repetition - therefore happier, more productive staff
- Less inaccuracy - therefore a higher, more consistent quality of output
- Less risk - therefore a safer, more scalable business overall
So what is there to lose? Try out one of these techniques and let us know how you get on.
Write a comment.